October 4, 2024

Sweden Timber acquires Aspa Bruk from Ahlstrom
Sweden Timber has signed an agreement to acquire Aspa pulp mill. Pulp from Aspa mill is used in a number of special applications. This complements and strengthens Sweden Timber’s position on the global market. This is completely in line with Sweden Timber’s strategy to be an obvious alternative for all the customers’ needs.
Sweden Timber is a Swedish owned company that produce wood, paper and woodcomposite products for a global market. The business today consists of sawmills, planning mills, paper mill and production of granulate in biocomposite where wood replace plastic. Aspa pulp mill produces bleached and unbleached softwood pulp that is used in a broad range of applications in paper and sold globally. It has an annual capacity of approximately 200 000 tonnes and 174 employees.
The acquisition of Aspa will be another step in our strategy to continue growing and developing the company. Through this acquisition, Sweden Timber broadens its existing product portfolio containing paper, wood products and biocomposite with pulp. Together with the team at Aspa mill we will continue to provide high quality products to our customers.
About Sweden Timber
Sweden Timber is a Swedish owned company that produce wood, paper and woodcomposite products for a global market. The business today consists of sawmills, planning mills, paper mill and production of biocomposite granulate. Production sites are located in Malmbäck, Hjortkvarn, Skillingaryd, Mora and Hyltebruk.
More information about Sweden Timber: www.swedentimber.se, www.hyltepaper.com and
www.woodcompounds.com
For information contact: mikael@swedentimber.se Phone: +46 721 888 688
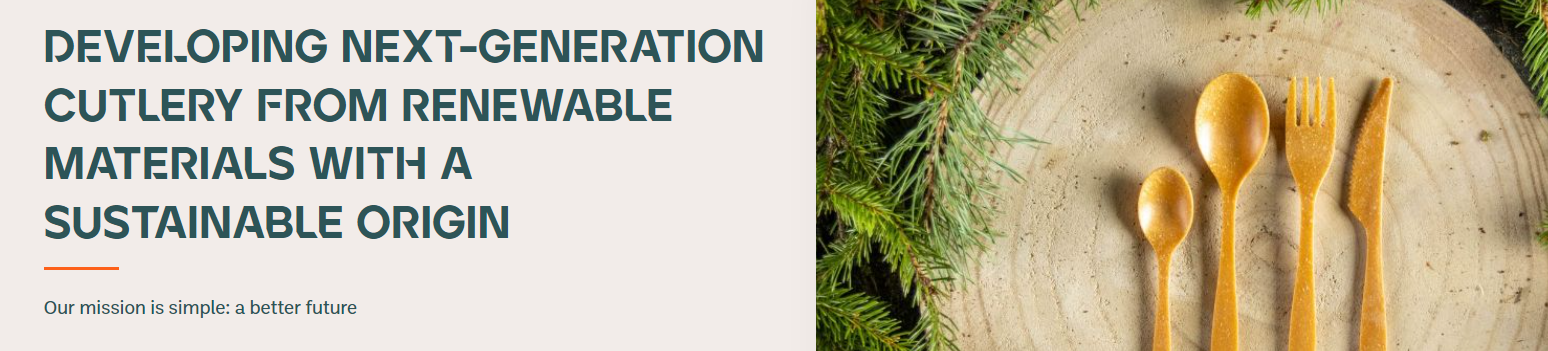
Woodcomposite Sweden AB are extending Strategic Partnership with Nature Line Cutlery Oy
Woodcomposite Sweden AB is excited to formally announce an extension of our collaboration with Nature Line Cutlery Oy through a long-term agreement. This partnership guarantees our continued supply of innovative and eco-friendly products.
Our commitment at Woodcomposite Sweden AB has always been to lead the way in sustainability within the industry. By deepening our relationship with Nature Line Cutlery Oy, we are not only securing the raw materials that meet our high standards but are also embarking on a joint venture in product development.
This extended collaboration will enhance the ability to provide consumers with renewable and sustainable cutlery options. We believe that through this partnership, more people will have the opportunity to choose reusable and environmentally friendly products for their daily use, aligning with our vision of reducing the ecological footprint.
Together, we are set to explore new frontiers in utilizing industrial side-streams, as well as renewable resources, to craft products that do not compromise on quality or the environment.
Discover more at Nature Lines website.
www.natureline.fi